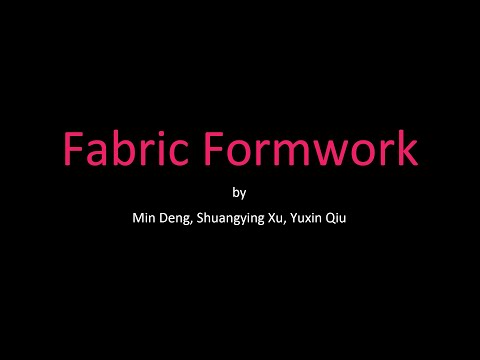
Traditional rigid formwork has distinct disadvantages for casting complex forms from concrete. Moreover, the wood formwork of a specific component can hardly be reused after disassembly. Fabric Formwork is a project focusing on developing a replicable linear concrete component manipulation method utilizing robotically-controlled, flexible fabric formworks. The method integrates design decisions into real-time adaptive fabrication and assembly processes, enhancing control over geometries and facilitating co-design between designers and the production and construction processes in an interactive way.
01 Project Information
Date: 06/2022 - 02/2023
Organization: ITECH Seminar Project, ICD, University of Stuttgart
Team: Shuangying Xu, Yuxin Qiu
Methods: 6-axis robotic adaptive casting, Agent-based Modeling, flexible formwork
02 Key Innovations
Flexible Formwork:
Create curving shapes with improved material efficiency and reusability, and support for real-time design adjustments.
Adaptive Fabrication Method:
Allow better control over geometries and interactive co-design between designers, machine and material.
03 Form Finding & Geometry Design
>> Geometry Generation
The design process starts with defining a geometry to form, followed by slicing it into reference curves in layers of the same height. To use the linear concrete component to form the geometry, a waving pattern is generated based on the reference curves' individual roughness. Here, we define the agents as control points of the curve. After segmenting the waving curve, components of each upper layer are defined by introducing a balance behavior to ensure the wall can be self-standing. Finally, each curve segment is aligned to the gravity orientation at the point of maximum curvature. The central curve of the unit to be fabricated is confirmed, and the unit is calculated based on the geometry's characteristics.

>> Design Space Exploration - Catalog
All reasonable possibilities were collected into a catalog of units standardized to 5 cm as fabrication choices, which will also serve as the design space. The average curve of each unit will be used to select the needed shape and compare it with the fabrication result. The catalog is then evaluated by the quality of the resulting geometry and classified. This process aims to make fabrication more controllable and improve efficiency.

The geometry catalog is established through a real-case fabrication experiment, where all reference points are tested and recorded. The results from both the physical and digital processes are then compared, forming a database to calibrate the average curve to the actual geometry shape.

04 System Control
>> Formwork and Robot Set-up
Lycra is sewn into a long tube ending with two wooden pieces. This tube is stretched and positioned by a robot arm as the formwork into which concrete is cast. This process translates the flexibility of fabric into flexibility in a pre-defined shape. A frame fixes the free end of the Lycra tube to maintain the formwork's length. A valve controlled by a servo is set inside the casting pipe to enable and disable the casting motion. A pressure sensor (RP-C10-ST) checks if the formwork is filled up.

>> ABM System & Behavior
The control points of the waving curve are identified as boid agents. The system is divided into digital and physical parts. The digital part decides the shape to fabricate based on behavior, while the physical part controls the accuracy of the fabrication process.

The positions of the boid agents control the forming of the waving curve. This curve is divided into segments, each with an individual maximum curvature point. The endpoints of these curves are determined, and based on the height and width differences, the KUKA TCP position is calculated.
Containment and separation behaviors are introduced in the digital part to ensure the agents form a proper waving curve. Additionally, to maintain the designed geometry in balance, a balancing behavior is defined. The agent will keep moving and seeking until there are at least four intersection points with the lower layer, stopping when there are four.

>> Shape Detection
Because of the unique gravity-defined shape of the units, we will never achieve exactly the same curve. The physical containment (5cm) allows the robot to slightly adjust the shape to get closer to the design requirements. A webcam will detect the real-time fabricating shape.
We use a seeking behavior to compare the real-time shape of the mid-curve with the designed one. When the average tolerance is less than 2cm and the maximum tolerance is less than 3cm, the adjusting process will stop, and the fabrication will be complete.

05 Fabrication and Assembly
>> Adaptive Forming Process
The real-time shape detection occurs throughout the entire fabrication and assembly process. During fabrication, it controls the tolerance and updates the physical fabricating results back to the digital simulation. During assembly, it checks if the assembly position is correct and identifies possible design changes. If the design is changed intentionally during assembly, the fabrication of the next component will be recalculated.

>> Assembly & Results

